SEAONYX
Research and redesign effort for the GenII SeaONYX Blow Out Preventer (BOP) control system HMI for offshore drilling.
This system is what stands between a clean, safe, successful drill effort and a potentially catastrophic environmental and crew safety disaster.

Team research and design effort with Karel Barnoski
Note / Due to the confidential nature of work at GE, this page provides a high level overview only. For a more detailed convesation about my work please get in contact with me

This is an offshore drilling rig. GE's Blow Out Preventer keeps it from exploding.
OVERVIEW
Late summer 2014 Karel and I were approached by Oil & Gas Drilling to explore a potential redesign of the HMI to accompany an upcoming BOP (Blow Out Preventer) system called SeaONYX.
Commissioned by a large drilling client, this new system was to become the baseline for all future installations.
In response we proposed a 2-step process:
1.
Research
August - December
We need to gain a solid understanding of how BOPs and their HMIs work, the context surrounding the current state of BOP and other rig HMIs, and most importantly we need to learn about the people who operate them.
2.
Design & Implementation
January - June
IF at the end of our research phase the team decided that a redesign was worthwhile, we'd work with engineering to generate:
-
An HMI Design System for SeaONYX
-
An accompanying set of Design Guidelines for future use
Karel and I ended up spending two weeks doing research in South Korea with two clients that had rigs undergoing commissioning and sea trials. We then spent another week living on-board an actively drilling rig in the Gulf of Mexico.
In January, for the implementation phase, Karel began to drop off and I completed the project through the end of June - meeting all of our deadlines and deliverables.

We weren't in the market of doing design for the sake of design.
The existing HMI looked confusing to us, but we weren't sure what - if anything - really needed to change.
DESIGN HYPOTHESIS & GOALS
We start with a hypothesis to structure our research and design efforts around testing:
We believe building an intuitive, innovative, and operator-focused SeaONYX system for BOP operators to be able to monitor and control the BOP will achieve increased customer satisfaction and operator effectiveness.
1.
Determine usability of current system
2.
Gain understanding of user ecosystem to determine primary users and use-cases
3.
Construct a pivot of persevere hypothesis based on research results
4.
Work within bounds of engineering and API to build an executable design


CHALLENGES
Users are difficult to access in dangerous and highly regulated environments
In addition to obtaining other official documentation and getting customers to agree to let us perform the research, both Karel and I needed to become certified for offshore work through the Falck BOSIET (Basic Offshore Safety Induction and Emergency Training) which includes Safety Induction, Helicopter Safety and Escape (HUET), Sea Survival and First Aid, Fire Fighting and Self Rescue.
Technology limitations & existing guidelines
Design guidelines are set by API (American Petroleum Institute), ISO (International Standards Organization) and IOGP (International Association of Oil & Gas Producers). In addition to following these guidelines, our own system that enables the engineers to build the working product has inherent limitations on visual and functional capabilities. Space is also precious on a rig, and any screens or sensors need to exist in harsh environments.
Every BOP is different
The HMI is a highly customized system with highly trained personnel working on a near one-of-a-kind BOP. This means our solution can't be a one-off, but rather an entire comprehensive design guideline and library.



The 4-story BOP is lowered to the ocean floor prior to drilling. The BOP is controlled from the surface to regulate the immense pressure as a result of the drilling process. When a 'kick' happens, the BOP must be activated to control the pressure within 15 seconds to prevent catastrophe. The 2010 BP Deepwater Horizon spill in the Gulf of Mexico was a combined result of human error and BOP failure. test test

FSEs (Field Service Engineers) are most dissatisfied with the current design as they actually use 100% of the system. Regular operational users only access about 20%.

Because space and time on a rig is tight, Karel and I needed a way to carry the basics of everything we might need to conduct impromptu sessions while on board. These research binders had everything from whiteboards, stickies, scissors, markers, and paper to keep us organized and ready.

We worked with Subsea Engineers in South Korea to co-create new screens based off of the existing screens. A group adverse to change, we had to pivot our research strategy a few times to get results.
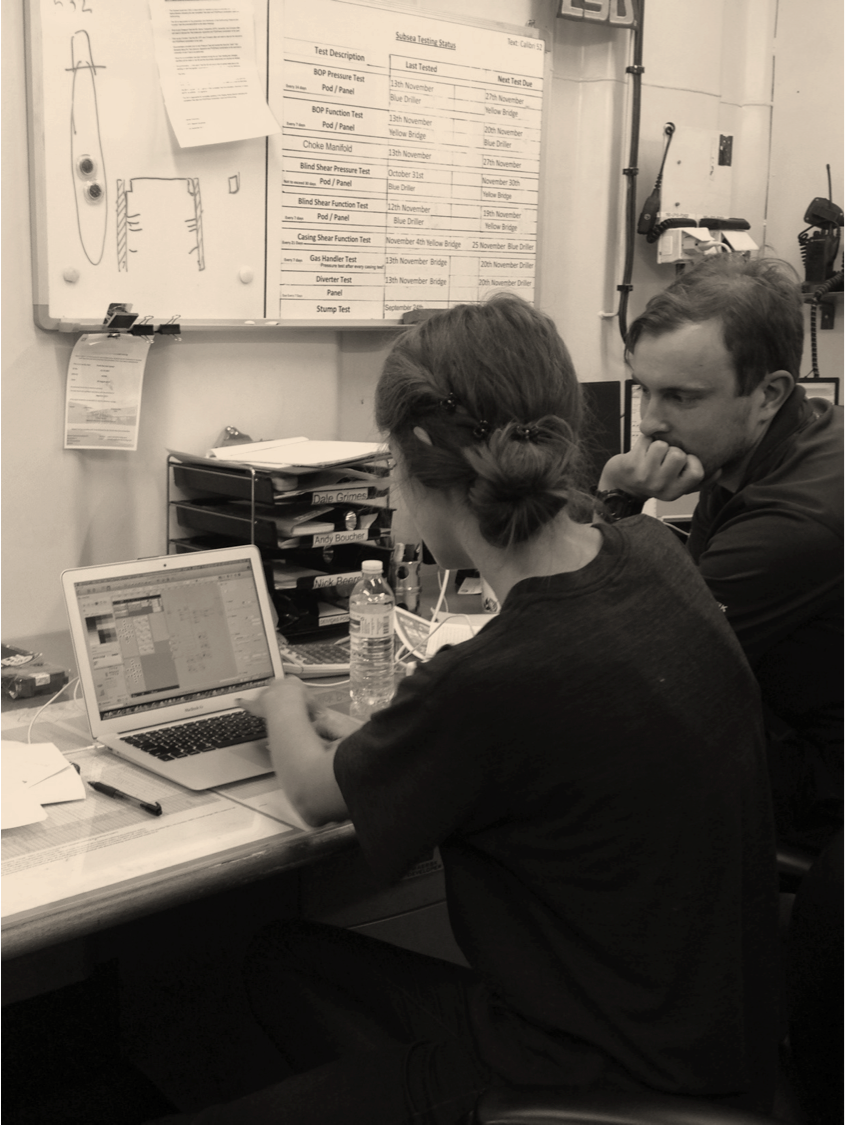
While living on board a rig in the Gulf of Mexico for a week we spent the bulk of our time observing and co-creating with drillers and subsea engineers (our primary users). With access around the clock, we developed a close relationship and co-creation methodology.
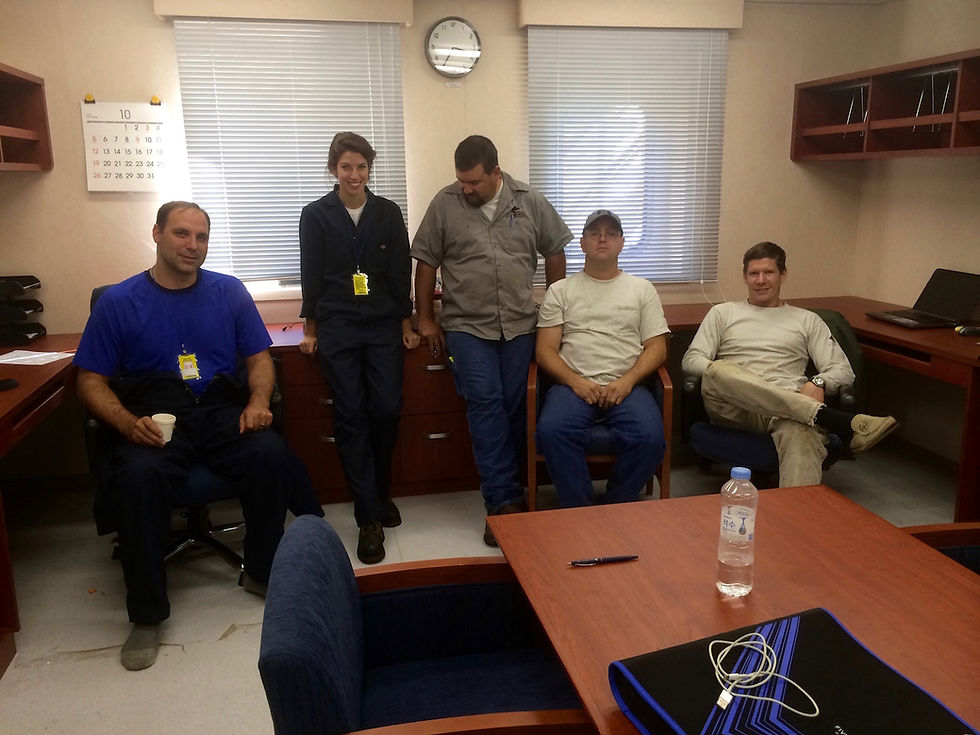
Karel and myself with the Subsea Engineering Team after a successful few days of research onboard in South Korea. Offshore workers are 7 times more likely to die on the job than the average worker. - Center for Disease Control & Prevention statistic, 2013 Subsea Engineers are our primary users. They work day and night to maintain the BOP and ensure its operation to the highest standard. Their work is both physically and